The railroad stands as one of America’s greatest technological achievements, transforming from humble wooden tracks into a sophisticated rail network that spans 140,000 miles across North America. The federal government played a crucial role in the development and regulation of the railroads, especially during critical times like World War I. From the thundering power of the legendary Big Boy locomotives to the precision of modern automated systems, nearly every aspect of railroad technology has evolved dramatically—except for one crucial component that remains frozen in time: the railroad tie.
Transcontinental Railroad: The Evolution of American Rail
Consider the major moments of railroad innovation, starting from the first transcontinental railroad, completed with the Golden Spike. This marked a significant milestone in American history, and the Pacific Railway Act provided federal support through land and loans once signed by President Abraham Lincoln in 1862. Then, in the 1940s, the iconic Big Boy No. 4014 rolled onto the tracks. Weighing 1.2 million pounds, it represented a leap in engineering that truly showcased American ingenuity. During its remarkable 20-year service life, this mechanical marvel covered over a million miles, demonstrating the industry’s capacity for groundbreaking advancement 80 years ago.
And similar progress has touched virtually every aspect of modern railroading.
Rail Safety: Enhancing Locomotives and Signaling
When we look at locomotives, we see the evolution from early steam engines—which played a crucial role in the development of locomotives—to diesel-electric powerhouses and emerging battery-electric options. The steam locomotive is particularly significant in the history of rail transportation, marking key periods such as the early 19th century and the post-WWII era before the industry largely transitioned into diesel. Signaling has also upgraded from manual switches to Positive Train Control (PTC) and automated systems, while operations have also moved from manual scheduling to precision scheduled railroading.
Advances in Track Monitoring and Safety Systems
Track monitoring’s visual inspections are beginning to explore AI-powered predictive maintenance and other technological advances while rail safety systems look into adopting advanced computer-controlled networks.
Leveraging Technology to Move the Rail Industry Into the Future
The railroad industry’s journey of innovation extends far beyond the iconic Big Boy. Modern freight locomotives now pull trains stretching over two miles long, powered by sophisticated computer systems that optimize fuel efficiency and performance. These technological marvels can generate up to 4,400 horsepower—enough to move one ton of freight 480 miles on a single gallon of fuel, making rail the most efficient form of ground transportation. The industry is also making significant efforts to reduce greenhouse gas emissions through technological advancements. A key goal is to achieve net-zero emissions by 2050, emphasizing the transition to low- and zero-emission technologies.
Additionally, the industry’s embrace of technology has transformed every operational aspect. Modern dispatch centers resemble NASA control rooms, with operators managing trains across thousands of miles of track through digital interfaces. As mentioned above, automated inspection portals use machine learning, high-speed cameras, and other advanced technologies to examine passing cars from every angle, detecting potential issues before they become problems. Further, trackside sensors monitor wheel bearing temperatures, track geometry, and rail wear in real-time, feeding data into predictive maintenance systems to enhance operational efficiency and safety.
Even traditional maintenance practices have been revolutionized. Drones now inspect bridges and remote sections of track, while ground-penetrating radar assesses ballast conditions beneath the rails.
Timeline: Railroad Innovation Through the Ages
[Image: Visual Timeline]
To better understand the current railroad landscape and plan for the future, it’s important to look back on the industry’s history, outlining key dates and milestones that laid the foundation for modern trains and operating systems.
1820s-1830s: First American Railroads Begin Operations
Early American Railroads
- Wooden rails with iron straps
- Basic steam locomotives
- Manual operations and signals
1860s: Pacific Railway Act and the Expansion of Railroads
- Introduction of creosoted wooden rail ties
- Steel rails begin replacing iron
- Telegraph-based dispatching
1940s:
- Introduction of diesel locomotives
- Big Boy steam locomotives showcase peak steam technology
- Wood rail ties remain unchanged
1980s-1990s:
- Computer-aided dispatching
- Advanced braking systems
- Wood ties continue as rail industry standard
2020s:
- Battery-electric locomotives emerge
- AI and automation transform operations
- 93% of ties still made from wood treated with creosote
The Price of Stalling Rail Tie Innovation
Beneath the railroad industry’s impressive innovations, improvements, and potential upgrades lies a foundation that hasn’t changed since the Civil War era: wooden rail ties treated with creosote, a practice that began in Europe and dates back to 1853. While the industry’s technological advancement has been remarkable in many areas, the continued reliance on wooden ties comes at a significant cost:
- With approximately 3,000 railroad ties per mile, the rail industry installs an estimated 23 million wood ties each year
- Approximately 6 million mature trees are cut down each year for tie production
- Replacement cycles span 8-12 years in high-decay zones
- Rising environmental concerns about creosote use
The cost of maintaining the status quo extends beyond environmental impact. Railways face escalating operational challenges that directly affect their bottom line:
Rising Labor Costs
Frequent tie replacement cycles require substantial workforce deployment, with each replacement operation disrupting normal track operations.
Safety Considerations
Working with creosote-treated wood ties requires special handling procedures and protective equipment for maintenance crews.
Supply Chain Vulnerability
Dependence on mature hardwood creates supply chain risks as quality timber becomes increasingly scarce.
Asset Depreciation
While wood ties are depreciated over 30 years on balance sheets, their actual service life in challenging environments often falls short, leading to premature asset write-offs.
Disposal Expenses
End-of-life disposal costs for treated wood ties continue to rise, typically reaching $10 per tie and climbing due to environmental regulations.
Composite Ties Line the Path Forward
The railroad industry’s strength lies in its ability to adapt and evolve. Just as the transition from steam to diesel transformed operations, the shift from wood to advanced materials like Evertrak’s composite ties made from Glass Fiber Reinforced Polymer (GFRP) represents the next frontier in rail infrastructure innovation.
Modern composite ties are more than just a material upgrade—they offer a comprehensive solution to multiple industry challenges:
Operational Excellence
- Consistent material properties eliminate the variability inherent in natural wood
- Greater resistance to lateral forces improves track stability
- Enhanced spike retention reduces maintenance requirements
- Superior performance in extreme weather conditions, from desert heat to sub-zero temperatures
Financial Benefits
- Extended service life significantly reduces total cost of ownership
- Reduced maintenance frequency minimizes track downtime
- Elimination of chemical treatments reduces handling and storage costs
- Potential for recycling at end of life creates additional value stream
Future-Ready Infrastructure
- Compatible with existing installation equipment and methods
- Engineered to meet or exceed all current industry standards
- Potential for embedding smart sensors for track health monitoring
- Scalable manufacturing process ensures consistent supply
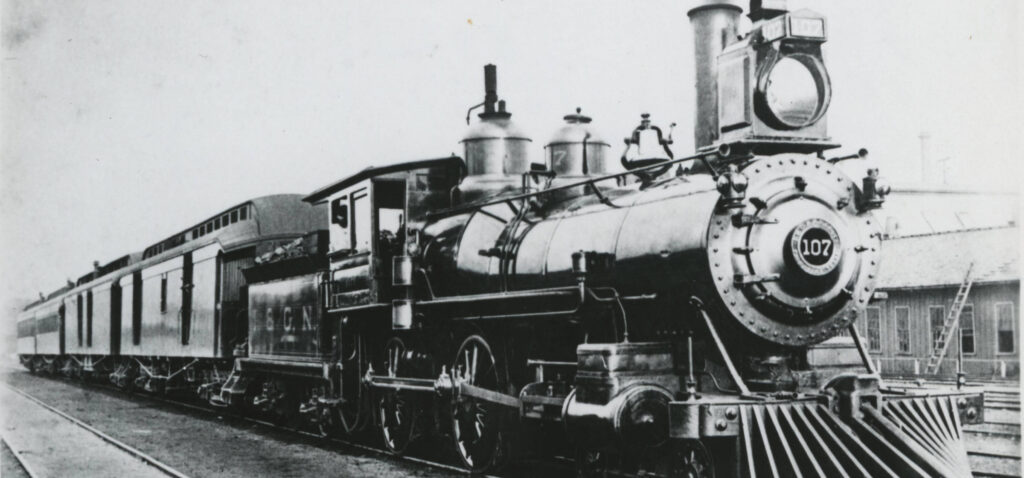
Embracing Railroad History and Change
Big Boy’s current surge in popularity is just one way the railroad innovations of the past are carving a path for future advancement. Following a multi-year restoration project, Union Pacific launched Big Boy on a “Heartland of America Tour.” Throughout this tour, Big Boy showcased its traditional features and modern upgrades at each stop along its route.
From Big Boy to Today
The spirit of innovation that gave birth to Big Boy and revolutionized railroad operations still thrives today. As the railroad industry faces new challenges—from environmental pressures to operational efficiency demands—the time has come to apply that same innovative spirit to the fundamental building blocks of our rail infrastructure: the railroad tie.
The future of American railroading depends not just on advancing the visible technology above the tracks but also on revolutionizing the foundation that supports it all. By embracing new materials and methods for railroad ties, the industry can honor its legacy of innovation while building a more sustainable and efficient future for rail transportation.