Plastic Free July® is a global movement that helps millions of people be part of the solution to plastic pollution—so we can have cleaner streets, oceans, and beautiful communities. Today, companies are rethinking traditional practices to reduce plastic waste and increase sustainability efforts, and we at Evertrak have joined the movement to do our part.
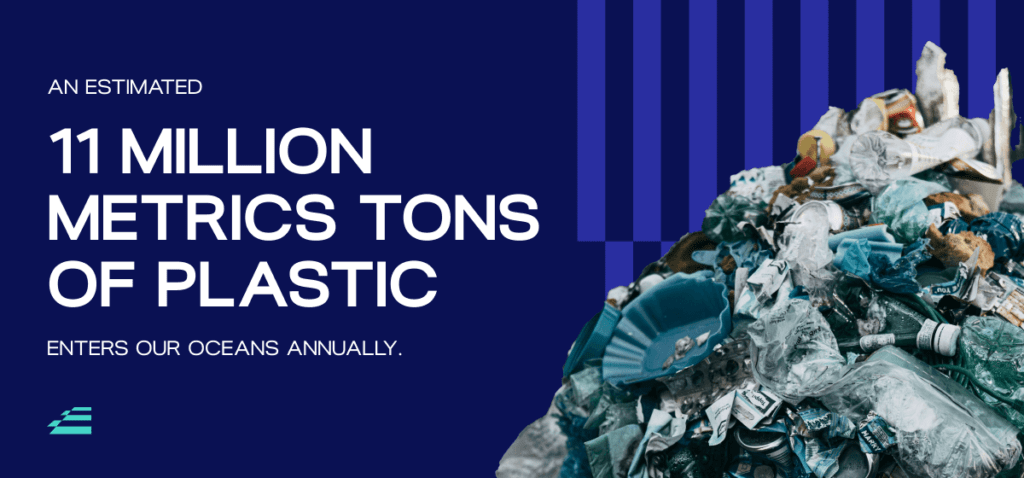
Globally, the scale of plastic pollution is staggering, with an estimated 11 million metric tons of plastic entering our oceans annually. While initiatives like Plastic Free July encourage individuals and organizations to reduce plastic consumption, the magnitude of the problem calls for reimagining how we use and repurpose existing plastic waste.
Many traditional industries face environmental challenges that are often overlooked in broader sustainability conversations. The railroad sector, with practices established long before environmental concerns became mainstream, presents unique opportunities for innovation that could contribute to larger environmental goals.
At this intersection of global plastic pollution and industry-specific operational challenges lies a railroad tie solution that tackles both issues at the same time. This approach not only addresses the acute pain point of status quo products that do not perform for the railroad industry but also demonstrates how creative problem-solving can turn existing plastic waste into solutions at scale.
The Plastic Paradox in Railroad Infrastructure
For nearly two centuries, the railroad industry has relied on wood railroad ties. Early ties were made from centuries-old hardwood that was incredibly resilient, and later ties were treated with creosote to extend the tie life. Current industry estimates for North America suggest 20 million wood ties are replaced annually—equivalent to approximately 6 million trees. Of the 20 million ties replaced annually, 4-6 million ties replaced are less than 12 years old.
This reliance on wood ties is much more than an environmental concern—it’s an operational challenge for railroads that impacts service to customers and financial results, like operating ratio (OR). OR is a key metric that measures how effectively a company uses its assets, demonstrated as a company’s operating expenses as a percentage of revenue. The frequent need for replacement disrupts operations and increases maintenance costs. Ties that are replaced faster than depreciation schedules create impairment charges on the balance sheet.
Why? All the centuries-old trees have been harvested, leaving new-growth trees that are not fit for purpose. Old-growth wood—and now, new-growth wood soaked in chemicals like creosote—made railroad ties more durable. Those days are over. This decline in quality further exacerbates the replacement cycle, creating a vicious circle of resource consumption that is catching up with operations.
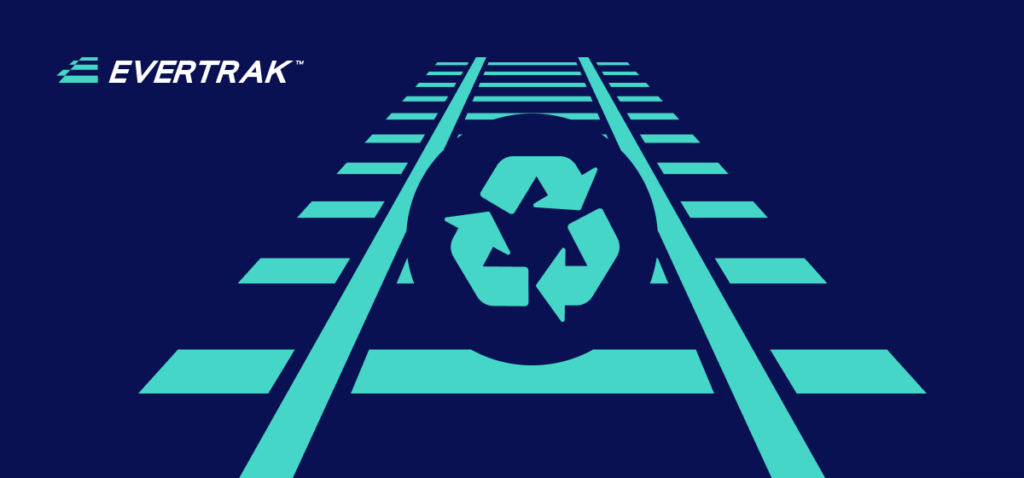
A Sustainable Solution: Composite Railroad Ties Made from Recycled Plastic
In response to these challenges, we developed Evertrak 7000.
Today, only 9% of plastic waste is effectively recycled globally, but we can change that with Evertrak 7000. We are committed to reducing plastic waste by using existing plastic that is diverted from our landfills and oceans. Our production of 1 million ties per year can sequester 180 million pounds of plastic while preventing the deforestation of 250,000 mature trees.
Despite the chronic pain caused by the lack of alternatives for wood ties, the railroads have traditionally been measured in their adoption of composites—mainly because composites didn’t deliver the performance. Our Glass Fiber Reinforced Polymer (GFRP) railroad ties are the exception. Our GFRP ties have the past performance to prove their durability and value, whether on the test track, where we have accumulated 700MGT, or in use on revenue generating roads with Class 1 railroads.
Through Evertrak 7000, we’re proving that it’s possible to repurpose the plastic we already have into long-lasting, functional infrastructure.
With plastic, the forest is right outside our door. Let’s use it.
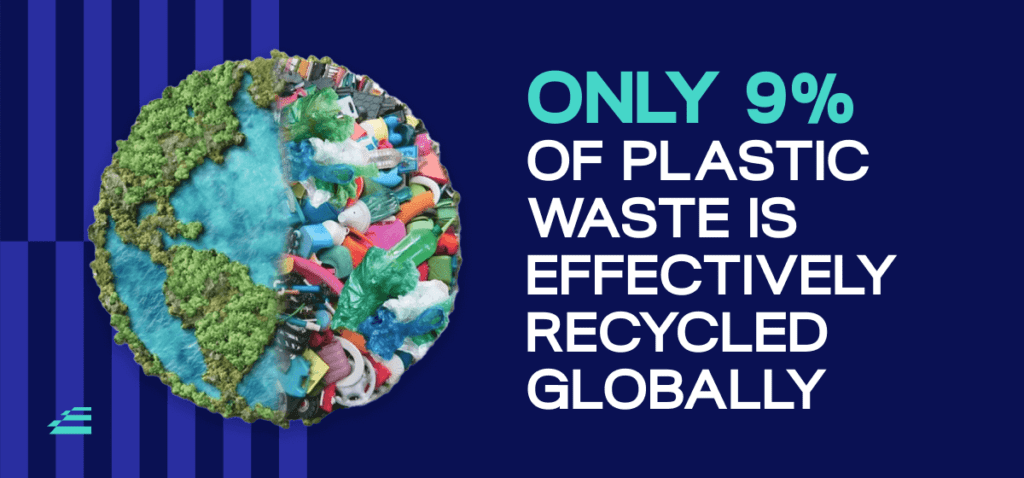
A Holistic Approach to Sustainability
The innovation in railroad ties made from recycled plastic goes beyond simple recycling. These ties are designed to last decades—five times longer than traditional wood ties in high decay zones. This longevity reduces the frequency of replacements, thereby decreasing the demand for new materials over time.
Moreover, Evertrak 7000 addresses multiple environmental concerns. Replacing wood ties helps to preserve forests, which act as vital carbon sinks and biodiversity hotspots. These sustainable ties also eliminate the need for toxic chemicals like creosote, reducing the risk of soil and water contamination.
We move beyond “closed-loop” recycling, sequestering carbon for decades. Plastic used in Evertrak ties won’t return to landfills, where less than 10% of plastic is recycled. When our ties eventually reach the end of their lifespan, they can be recycled and reformed into new ties, further reducing the need for virgin plastic. In this way, we are helping build a “plastic mine” that has residual value long into the future.
But how much plastic does Evertrak actually remove from landfills? Unlike consumer applications that may use ounces or pounds of recycled plastic in their products, we use tons of plastic at scale. At 4 million Evertrak railroad ties a year—a low-end estimate of the number of wood ties rotting out in less than 12 years—the industry would sequester 720,000,000 pounds or 360,000 tons of plastic annually. That’s the size of a medium landfill.
A Model for the Future
This approach to railroad infrastructure serves as an example of how industries can rethink their relationship with plastic. By repurposing existing plastic waste, extending product lifespans, and creating circular economy models, it’s possible to address the plastic crisis while still meeting critical infrastructure needs.
Industrial applications like railroad ties will increase the demand for hard-to-recycle plastic, and this demand should stimulate supply.
Plastic Free July may be over, but our innovation lasts forever and demonstrates just one of the many ways organizations can leverage and repurpose the plastic we’ve already produced while avoiding the use or production of new plastic. At Evertrak, we believe in creative thinking and are committed to coming together to solve real industry pain points, turning the tide on plastic waste, and setting new standards for sustainability across industries.