For nearly two centuries, railroad ties have formed the literal foundation of North America’s 140,000-mile rail network. These humble components, often overlooked but absolutely critical, have remained largely unchanged since the Civil War era—most still made from wood treated with creosote, a practice dating back to 1853.
While locomotives evolved from steam engines to sophisticated diesel-electric powerhouses, and operations transformed from manual scheduling to precision computer-controlled systems, the railroad tie has remained frozen in time.
This technological stagnation comes at a significant cost. Each year, the railroad industry installs approximately 23 million wood ties, requiring around 4–6 million mature trees to be harvested annually. These ties frequently need replacement every 8–12 years in high-decay zones, creating a continuous cycle of installation, maintenance, and disposal that consumes resources and disrupts operations.
So, what’s the solution? Replacing wood ties with a better, more durable material that doesn’t leech harmful chemicals into the surrounding environment.
The Composite Journey: Early Challenges in Railroad Tie Innovation
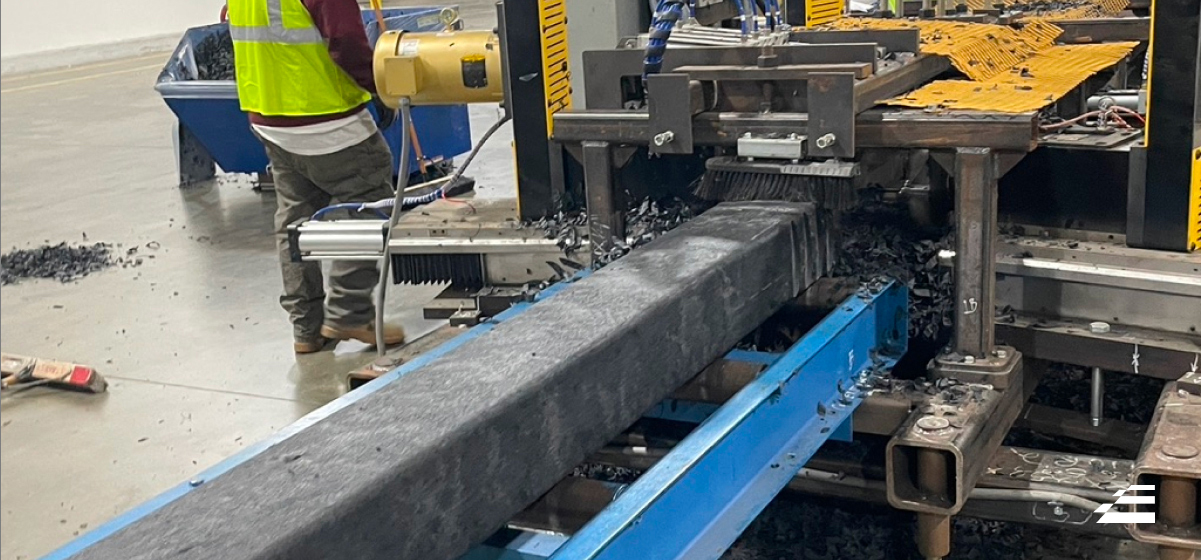
Attempts to develop viable alternatives to wood railroad ties began decades ago as the industry recognized the limitations inherent in traditional materials. Composite materials appeared promising, offering the potential for custom-engineered properties and superior resistance to environmental degradation. However, these pioneering efforts encountered substantial obstacles that prevented widespread adoption.
Early composite railroad ties simply couldn’t match wooden ties in performance characteristics crucial for rail operations. When subjected to the intense stresses of heavy rail traffic—including substantial vertical loads, lateral displacement forces, and constant vibration—many first-generation composite ties exhibited premature structural failures that raised serious operational concerns.
Quality control presented another significant hurdle. Manufacturing processes for these early composite alternatives often produced inconsistent results, with substantial performance variations between individual ties. For railroad engineers who prioritize predictability and reliability, this inconsistency made composite ties difficult to integrate into existing infrastructure systems.
Further, the combination of questionable durability and higher acquisition costs made early composite ties economically unattractive. Without demonstrated long-term performance benefits, railroad operators remained reluctant to invest in these more expensive alternatives, particularly given the industry’s conservative engineering philosophy that prioritizes proven technologies over experimental solutions.
These initial disappointments created a reputation problem that continues to affect the adoption of composite tie technology today. Companies introducing advanced composite solutions must overcome both technical challenges and deeply entrenched skepticism from industry decision-makers who remember the shortcomings of earlier attempts.
Engineering the Next Generation: Breakthroughs in Composite Railroad Tie Technology
Despite these early setbacks, ongoing research and development in materials science has produced remarkable advancements in composite railroad tie technology. Contemporary solutions like Evertrak’s Glass Fiber Reinforced Polymer (GFRP) ties represent a fundamental departure from previous composite designs, offering performance characteristics that address and overcome the limitations of both wood ties and earlier composite attempts.
Modern engineering approaches have dramatically improved structural performance. Today’s advanced composite ties deliver superior strength characteristics compared to traditional hardwood ties, particularly in their ability to maintain these properties throughout their service life rather than degrading over time. Their resistance to moisture infiltration, insect damage, and biological decay ensures consistent performance even in the most challenging operational environments.
Manufacturing technology has similarly evolved. Computer-controlled production systems and sophisticated quality assurance protocols now ensure remarkable consistency between individual ties. This uniformity gives railroad engineers the confidence to incorporate these components into critical infrastructure, knowing they’ll perform predictably across thousands of installations and decades of service.
Perhaps most significantly, contemporary composite ties offer extraordinary longevity compared to traditional alternatives. While conventional wood ties typically require replacement within 8–12 years depending on environmental conditions, advanced composites like the Evertrak 7000 can provide reliable service for up to five decades—even in demanding settings. This extended service life fundamentally changes the economic equation for railroad operators, offsetting higher initial acquisition costs with dramatically reduced lifecycle expenses.
Comparing Materials: The True Advantages of Modern Composite Railroad Ties
Guided by rigorous testing procedures, composite ties have proven their capabilities across performance standards, sustainability efforts, and total cost of ownership.
Performance Superiority: Engineering Reliability into Railroad Infrastructure
The performance differential between wood and advanced composite railroad ties becomes increasingly evident when examining their long-term characteristics. Wood ties exhibit substantial variability not only between different species but even within the same timber type. Initial strength may be adequate, but environmental factors progressively degrade this performance through splitting, moisture absorption, fungal decay, and mechanical wear at plate seats.
Evertrak’s engineered composite ties deliver precisely calibrated mechanical properties that remain stable throughout their service life. Their resistance to the forces encountered in everyday railroad operations—including dynamic loads from passing trains, lateral displacement pressures, and fastener retention requirements—remains consistent rather than declining progressively as with organic materials.
The maintenance profiles of these materials differ dramatically as well. Wood ties demand ongoing inspection and periodic chemical treatment from harmful ingredients like creosote to extend their useful service life. As they age, they often require additional maintenance interventions like spike hole plugging preservative application, and eventually complete replacement. Modern composite alternatives require minimal maintenance beyond standard track inspection procedures, maintaining their dimensional stability and mechanical properties without additional chemical treatments or specialized attention.
Environmental Considerations: Sustainable Solutions for Railroad Infrastructure
The environmental implications of railroad tie selection extend far beyond the immediate rail corridor. Traditional hardwood tie production places significant pressure on forest resources, requiring millions of mature trees annually. Even with replacement procedures in place, hardwood growth cycles span decades, with the demand for ties contributing to deforestation concerns across timber-producing regions.
Advanced composite alternatives like Evertrak’s ties transform this environmental equation by incorporating recycled materials into their manufacturing process. By diverting plastic waste from landfills and repurposing it into durable infrastructure components, these products simultaneously address waste management challenges and reduce pressure on forest ecosystems.
As mentioned above, creosote treatment of wood ties represents another significant environmental concern. This preservative, while effective at extending wood tie service life, contains numerous hazardous compounds that can migrate into surrounding soil and groundwater over time. Additionally, workers handling these treated ties face potential health risks from chemical exposure during installation and maintenance operations. Composite alternatives eliminate these chemical preservation requirements entirely, removing a significant source of potential environmental contamination and occupational hazards.
End-of-life considerations further differentiate these materials. Creosote-treated wood ties present disposal challenges, as their chemical content makes them unsuitable for most recycling applications. Many ultimately enter landfills where they continue releasing preservative chemicals into the environment. In contrast, Evertrak’s composite ties maintain recyclability at the conclusion of their service life, representing a recoverable asset rather than a disposal liability and supporting circular economy principles.
Economic Analysis: The Compelling Business Case for Composite Railroad Ties
The financial implications of railroad tie selection extend far beyond initial acquisition costs. While wood ties typically offer lower upfront purchase prices, their total lifecycle costs often prove substantially higher when accounting for installation labor, maintenance requirements, operational disruptions during replacement, and disposal expenses.
Advanced composite ties like Evertrak 7000 present a different economic profile. Their higher initial investment delivers remarkable long-term returns through dramatically extended service life, reduced maintenance requirements, and minimized operational disruptions. When analyzed through comprehensive total cost of ownership methodologies, these composite solutions frequently demonstrate substantial savings compared to traditional wood alternatives, particularly in challenging environmental conditions where wood tie degradation accelerates.
Operational efficiency represents another economic dimension often overlooked in traditional cost analyses. More frequent tie replacement cycles with wood ties necessarily increase track downtime, reducing network capacity and potentially disrupting service commitments. The resulting impacts on revenue generation, logistics operations, and customer relationships can far exceed the direct costs of materials and labor. Evertrak’s long-lasting composite ties minimize these operational disruptions, supporting more consistent and reliable rail operations.
Regulatory considerations increasingly factor into the economic equation. As environmental standards continue evolving, materials requiring hazardous chemical treatments face growing regulatory scrutiny and potential compliance costs. Sustainable alternatives like Evertrak’s composite ties help railroads future-proof their infrastructure against evolving regulatory requirements while demonstrating environmental stewardship to customers, communities, and investors.
Pioneering Rail’s Future: The Path Forward for Railroad Infrastructure
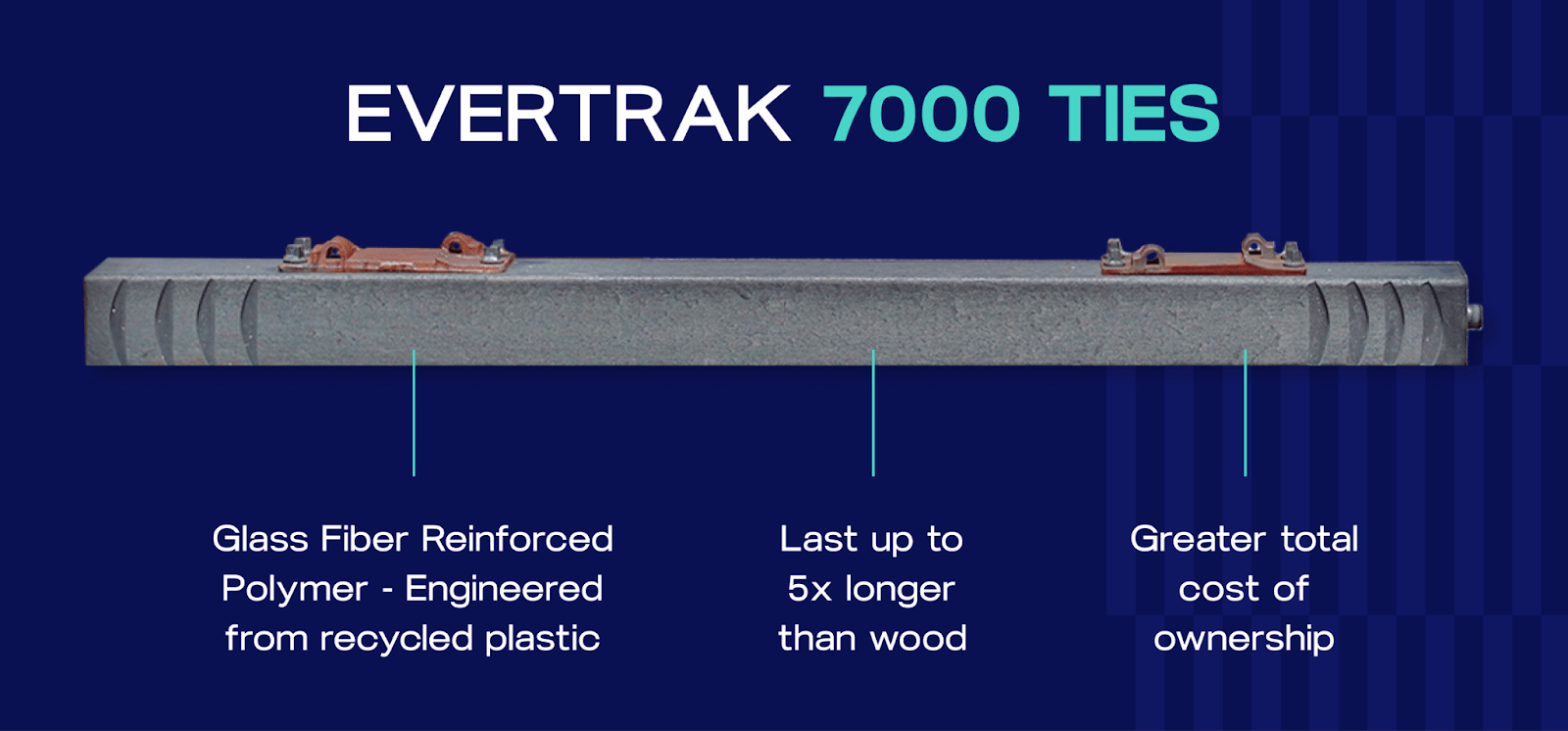
The railroad industry stands at an inflection point where infrastructure decisions made today will shape operational capabilities, economic performance, and environmental impacts for decades to come. While wood ties have served the industry for generations, mounting challenges related to resource sustainability, environmental considerations, and long-term economics make this traditional approach increasingly problematic.
Evertrak’s advanced composite ties represent a forward-looking solution that addresses these multifaceted challenges. Engineered from recycled plastic, these Glass Fiber Reinforced Polymer (GFRP) ties deliver exceptional strength and durability that matches or exceeds the performance of premium hardwood alternatives. Their dramatically extended service life—approximately five times longer than conventional wood ties—translates into significant reductions in replacement frequency, maintenance requirements, and operational disruptions.
These benefits extend beyond purely financial considerations. By eliminating creosote treatment requirements and reducing demand for hardwood timber, Evertrak’s composite ties advance the railroad industry’s sustainability objectives. Their manufacturing process diverts substantial quantities of plastic waste from landfills, contributes to circular economy principles, and reduces the industry’s overall environmental footprint.
With the North American railroad tie market projected to reach substantial growth in the next five years, material selection decisions carry immense economic and environmental implications. Plus, the comprehensive costs associated with traditional wood ties—financial, environmental, and operational—have become increasingly difficult to justify in an era of resource constraints and sustainability imperatives.
Embracing Railroad Innovation: Building Tomorrow’s Infrastructure Today
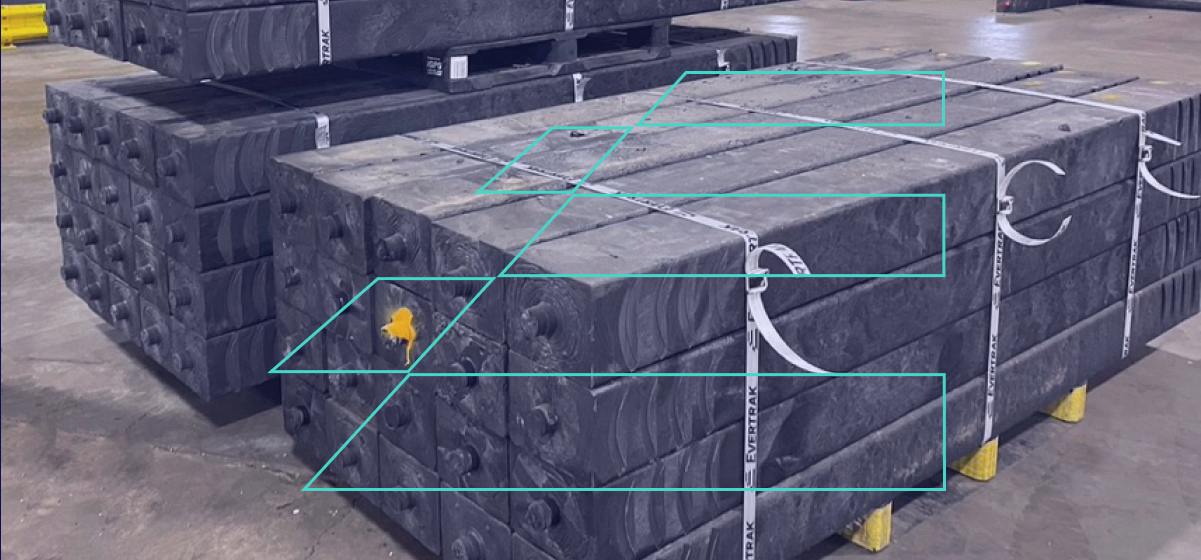
Throughout its history, the railroad industry has demonstrated remarkable capacity for technological evolution. This same innovative spirit must now extend to the fundamental building blocks of railroad infrastructure.
Modern composite railroad ties deliver comprehensive solutions to multiple industry challenges:
Operational Advantages
The consistent material properties of engineered composites eliminate the natural variability inherent in wood, providing predictable performance characteristics throughout their service life. Their superior resistance to lateral displacement forces enhances track stability under load, while improved fastener retention reduces ongoing maintenance requirements. These materials demonstrate exceptional performance across diverse environmental conditions, from warm climates to freezing temperatures.
Financial Sustainability
The extended service life of advanced composite ties fundamentally transforms their economic value proposition, dramatically reducing lifetime ownership costs despite higher initial acquisition expenses. Their reduced maintenance requirements minimize track outages and associated operational disruptions, while eliminating chemical treatment processes reduces handling costs and potential liabilities. Further, their recyclability creates additional value recovery opportunities at service life conclusion.
Future-Ready Design
Compatibility with existing installation equipment and methodologies facilitates smooth integration into maintenance operations without requiring specialized tooling or techniques. Engineered to meet or exceed all current industry performance standards, these ties provide immediate benefits while supporting future infrastructure development. Advanced manufacturing processes ensure consistent supply availability, reducing logistics challenges associated with natural material sourcing.
The spirit of innovation that propelled railroad technology forward—from the transcontinental railroad’s completion to the engineering achievements represented by iconic locomotives—must now extend to the fundamental components of track infrastructure. By embracing advanced composite tie solutions from Evertrak, the industry can honor its tradition of technological advancement while building a more sustainable, efficient, and resilient future for rail transportation across North America.