The railroad industry is moving forward, one mile of track at a time. As former chief engineers from major railroads gathered at Evertrak’s Engineering Summit in their state-of-the-art composite tie manufacturing facility, their message resonated loud and clear: the future of rail infrastructure demands bold thinking, calculated risk-taking, and a fundamental shift in how we approach track maintenance.
The panel discussion, featuring industry veterans with decades of combined experience, offered unprecedented insights into the challenges and opportunities facing composite tie adoption in North America’s vast railroad network.
The Expert Panel: Industry Veterans Leading Change
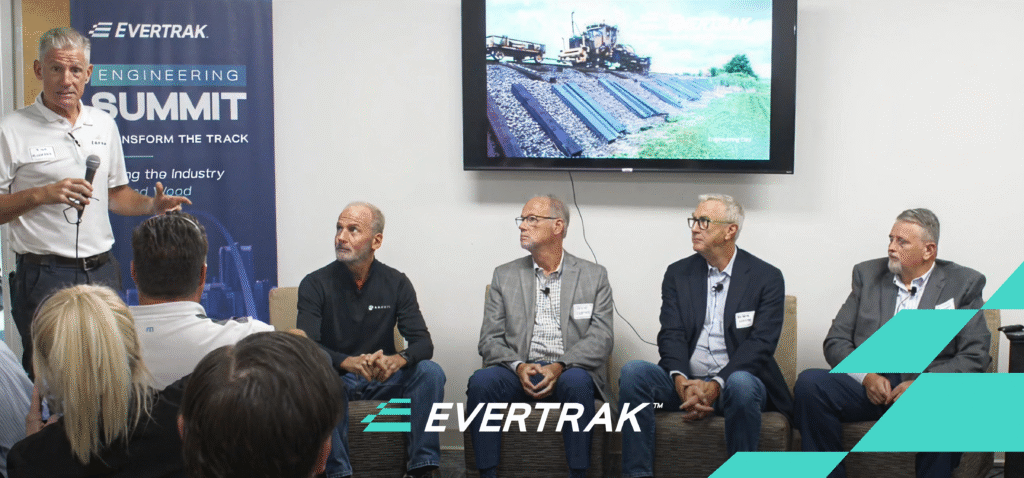
The discussion was moderated by Dennis Muilenburg, former Chairman and CEO of Boeing and current Evertrak board member, who brought his exceptional aerospace perspective on managing complex technological transitions. The panel featured some of Evertrakās top advisors: former VP of Engineering at Union Pacific David Connell, former VP of Engineering at Canadian Pacific Railway Brent Laing, and former Sr. VP of Operations at CSX Ricky Johnson.Ā
These expert engineers represent not just technical expertise, but the cultural shift happening within the railroad industry as it grapples with 21st-century challenges while operating on 19th-century principles.
The 30-Year Vision: Transforming Railroad Maintenance
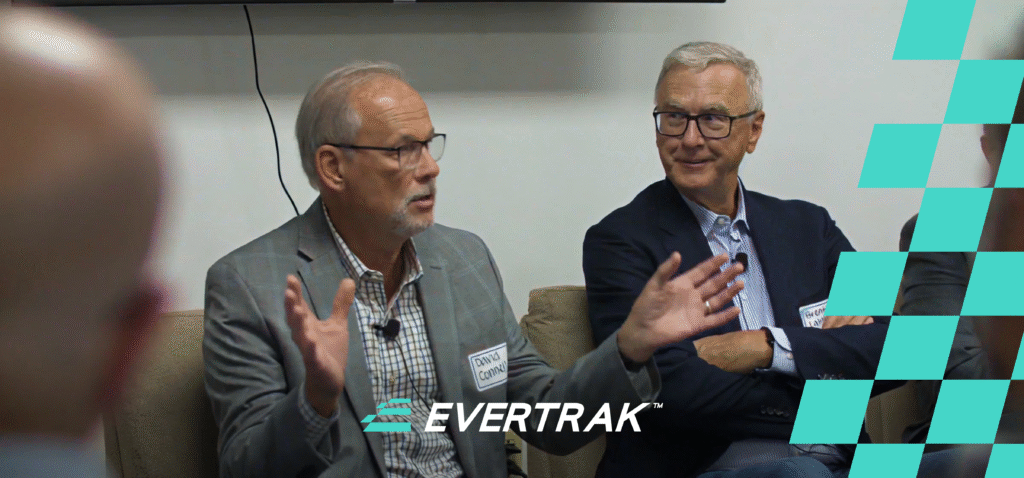
Connell opened the discussion by contextualizing composite ties within the broader history of railroad innovation. Drawing parallels to game-changing technologies like the Herzog ballast train with GPS technology and flange bearing frogs that last 10 times longer than traditional designs, he painted a picture of what true transformation looks like.
“When you think about a world where we aren’t showing up with a tagging every 5 to 7 to 8 years, taking the track down, interrupting customersā shipments, it is a really, really big deal,” Connell emphasized. This vision goes beyond mere material substitutionāit’s about fundamentally rethinking how railroads approach infrastructure maintenance.
The panel acknowledged this transformation won’t happen overnight. As Laing noted, “Transformational change is always difficult in the railway because it tends to be glacial.” However, he quickly added the industry has actually undergone significant changes in how it approaches infrastructure, even if these changes aren’t always visible to outsiders.
Breaking the Price-Over-Performance Paradigm
One of the most revealing moments came when Johnson highlighted a fundamental inconsistency in railroad procurement practices. While railroads willingly pay premium prices for high-quality rail from manufacturers like Sumitomo, the tie market has historically been driven purely by price.
“When you think about rail, we’re willing to pay extra for rail, but we’re not willing to pay extra for ties,” Johnson explained. “We will pay that premium because we’re not going to accept rail failing before its life cycle.”
This double standard has profound implications. The panel revealed engineering departments often find themselves trapped in a cycle where they must replace 2.6 to 2.8 million ties annually on major railroads, fitting this massive undertaking within fixed budgets. The easiest solution has always been to stick with the cheapest optionāwood ties treated with creosote.
But this approach is becoming increasingly untenable. Not only are there more options availableārubber, concrete ties, and other materialsāthe disposal costs of wood ties are skyrocketing as environmental regulations tighten. Johnson warned about the future when cogeneration plants can no longer burn creosote-treated wood ties: “When the cogen plants go and your price goes up five, 600% for disposal because you’re having to landfill, it’s a huge cost to the railroad.”
Quality Through Consistency: Better Than Wood Ties
What sets Evertrak apart from previous composite tie ventures became clear during the factory tour and subsequent discussion. Brent Laing was particularly impressed by the manufacturing consistency: “Looking at the production line, everything’s X-rayed, right? I know what I get and they do batch sampling, whereas you got a stack of the other product [wood ties], you don’t quite really know what you’re going to get because it can be five different species.”
This consistency represents a fundamental shift from the natural variability of wood products. The panel emphasized how Evertrak’s controlled manufacturing process, with its PLC-controlled batching and injection systems, delivers predictable performanceāa critical factor for infrastructure that must perform reliably for decades.
Learning from Past Attempts at Composite Railroad Ties
The panel didn’t shy away from discussing the elephant in the room: the failures of early composite tie attempts. Connell provided crucial context: “Those early startups were very constrained as most startups are. And, quite frankly, the cost was more than what we were trying to spec… They start dumbing down the product to where they can get the cost down for today’s cost.”
This race to the bottom led to longevity issues that created lasting skepticism within the industry. Johnson elaborated on this legacy: “Unfortunately, Evertrak is paying for the sins of some of the fly-by-night companies that we’ve all seen in our careers with composite tiesāwhere they’re here one year, they give us a product that fails 2 or 3 years, and they’re not even in business anymore.”
However, all three panelists agreed Evertrak has overcome these historical challenges. With 7-8 years of consistent manufacturing and proven field performance, the company has demonstrated composite ties can deliver on their promises.
Composite Ties: Beyond Traditional Applications
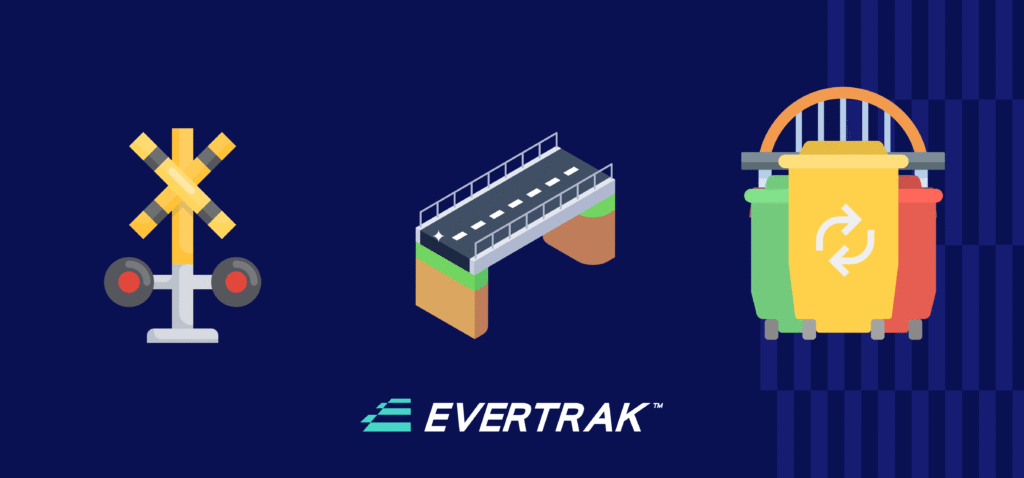
The discussion revealed exciting opportunities beyond traditional track applications. From improved service life to environmental benefits and installation improvements, the panelists identified several high-value use cases where composite ties offer compelling advantages:
Railroad Crossings
“If I had a dollar for every rough road crossing complaint,” Johnson quipped, highlighting one of the top two engineering complaints he received at CSX (the other being creosote ties stored along the right-of-way). Composite ties’ resistance to degradation under asphalt makes them ideal for these challenging applications.
Bridge Installations
Connell emphasized the economics: “Ballast deck bridges where unit costs are very high to get a cross tie placed on a bridge that has sides on itāthat’s not very easy.” The longer lifespan of composite ties makes the higher initial investment much more palatable in these difficult-to-access locations.
The Circular Economy
Perhaps most revolutionary is the concept of turning waste into assets. Evertrak’s ties are made from durable Glass Fiber Reinforced Polymer (GFRP) using recycled plastic. These reinforced composite materials can be recycled at the end of a tie’s service life. Laing explains: “It’s not a waste. It’s now an asset that can be reused in the next generation of ties.” This stands in stark contrast to the current model where millions of creosote-treated hardwood ties either go to increasingly regulated cogeneration plants or create what Laing called “big windrows of ties along your right of way… fire risk and everything else.”
Overcoming Implementation Barriers: The Real Economics
The panel provided frank insights into why adoption has been slow despite clear technical advantages. The core issue isn’t just about individual tie costsāit’s about how railroad capital allocation works.
Johnson broke it down: “You got X number of miles of track, you know, you got to replace 2.6 to 2.8 million ties per year… But at the same time, oh yeah, I got to go buy 75 locomotives at 4 million bucks a pop. So it’s competing interests.”
The panelists emphasized that success requires painting the complete picture of total cost of ownership. This includes:
- Disposal costs: Often buried in different departmental budgets
- Track downtime: Lost revenue from maintenance windows
- Maintenance frequency: The hidden costs of returning to the same subdivision every 5-8 years
- Environmental liabilities: Future regulatory risks from creosote and the impacts of wood ties rotting or degrading quickly in moist climates and high-decay zones
Connell suggested this might require strategic intervention: “It’s more of a strategic issue at a particular Class I where maybe an engineering department budget is subsidized to implement this new technology that’s going to take you to what that new vision will eventually deliver.”
The Human Element: Building the Right Team
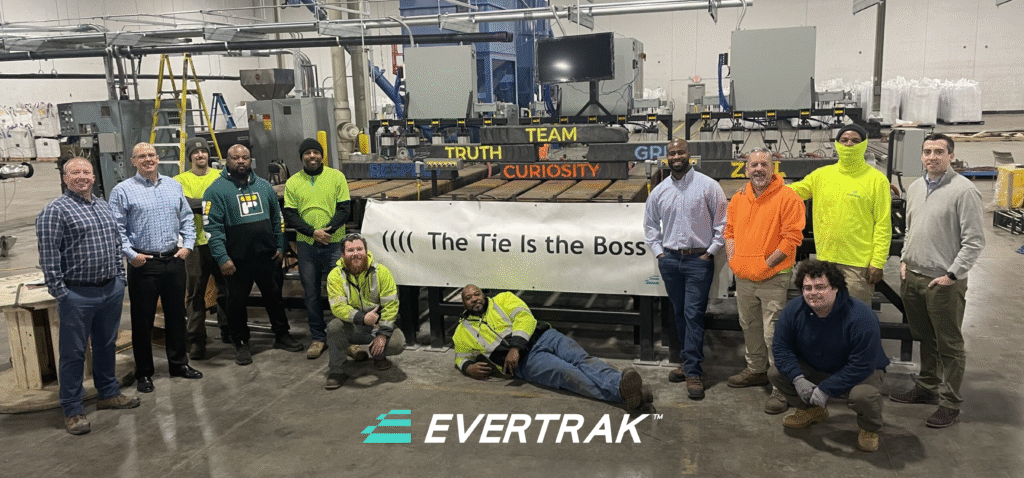
Muilenburg steered the conversation toward what ultimately matters most: people. When asked about the key characteristics for successful engineers in this industry, the responses were revealing.
Connell praised Evertrak’s culture: “The fact that they’re adopting lean, which I completely believe in… it shows how mature this workforce has become already. When you adopt lean, you involve the ideas of everybody in the manufacturing process.”
Laing emphasized the importance of listening and advocacy: “Engineers, we’re great. We usually have a pocket protector with a pen or two in it, and we tend to be socially inept,” he joked, before adding seriously, “I think the team is solid and they’re asking the right questions… It’s always, I think they’re in that listening mode.”
Johnson brought it back to core values: “It’s like my grandmother used to always tell me… ‘The truth will be welcome in heaven.’ Being truthful with one another… for that relationship to succeed between whoever the customer is, whatever railroad or entity, and Evertrak, it’s that truthfulness of where we’re heading.”
The Path Forward: Collaboration and Strategic Thinking
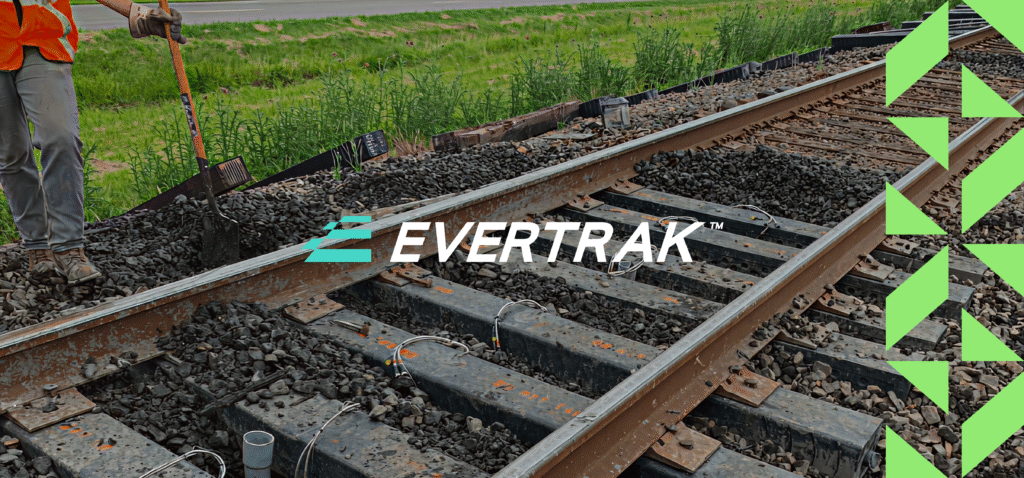
The summit’s message was unequivocal: the technology has matured, the quality is proven, and the economic case is strengthening. What’s needed now is collaborative partnership between innovative manufacturers like Evertrak and forward-thinking railroads willing to invest in long-term solutions.
The panel addressed a pointed question from the audience about why, given 50+ years of composite tie development, the major railroads remain “fixated on price.” The responses were illuminating:
- The issue sits at the intersection of engineering, procurement, and finance departments that often don’t coordinate effectively
- Environmental regulations will eventually force change, but waiting risks higher costs
- Success requires executive-level strategic decisions to subsidize early adoption
- The railroad industry’s critical infrastructure status means regulations are unlikely to force immediate change
As Muilenburg concluded, it ultimately comes down to people and valuesāintegrity, quality, safety, and the courage to embrace transformational change. The engineering community must lead this transition, not just as technical experts but as advocates for long-term thinking and sustainable solutions.
Looking Ahead: The Future of Railroad Ties
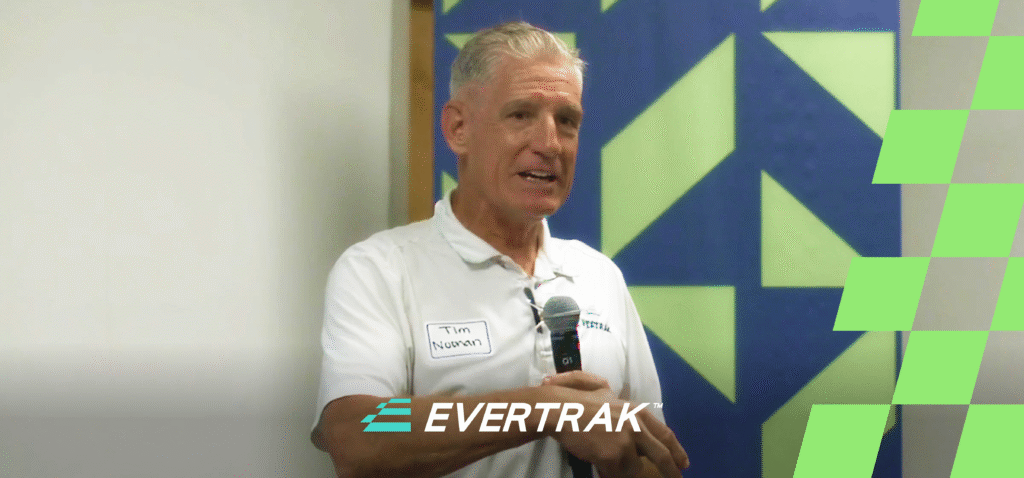
Tim Noonan, Evertrak’s CEO, closed the panel with a powerful reminder of what’s at stake. Pointing to the 50 employees on the factory floor, many of whom are formerly incarcerated citizens getting a second chance, he emphasized that this isn’t just about railroad tiesāit’s about sparking greatness in others and building a sustainable future.
Evertrak has assembled advanced manufacturing capabilities and a coalition of industry veterans, innovative thinkers, and dedicated workers all aligned around a common vision. As the railroad industry faces mounting pressure from aging infrastructure, environmental concerns, and evolving regulations, the question isn’t whether composite ties will become mainstream, but how quickly the industry can embrace this transformation.