For nearly two centuries, the railroad industry has relied on wood as the primary material for railroad ties, the critical components that support the rails and bear the weight of trains. However, as environmental concerns increase and the demand for more durable, long-lasting solutions grows, the industry must consider new materials as it looks toward the future.
Enter composite railroad ties—engineered alternatives that promise superior strength, longevity, and sustainability compared to their wooden counterparts.
What Are Composite Railroad Ties?
Composite railroad ties are the result of years of research and innovation in material science. These advanced ties are manufactured using a combination of recycled plastics, such as high-density polyethylene (HDPE) and polypropylene (PP), and they’re reinforced with high-strength fibers, typically glass or carbon. The carefully engineered blend of materials gives composite ties their unique properties, allowing them to withstand the intensity of heavy rail traffic while maintaining dimensional stability and resisting decay.
The most important benefit of composite ties is that they offer superior performance and better value than wood in a large majority of use cases in high decay zones. Simply state, over 30 years, an operator installs wood ties 4-5 times and Evertrak once. One and done.
Another key advantage of composite ties is their environmental friendliness. By utilizing recycled plastic to make these new ties, manufacturers like Evertrak are not only diverting waste from landfills and oceans but also reducing the demand for virgin materials. Evertrak’s composite ties are recyclable, positioning them as an asset rather than a liability in terms of disposal costs and sustainability. Moreover, composite ties eliminate the need for harmful chemical treatments, such as creosote, which are commonly used to preserve wooden ties. This means a safer working environment for railroad workers and a reduced ecological impact. And our composite ties don’t just offer superior environmental benefits. They last up to 50 years compared to treated wood ties, which must be replaced every 8-15 years.
The Evolution of Composite Ties
The quest for an alternative to wooden railroad ties is not new. Over the years, the industry has experimented with various materials, including concrete ties, steel, and earlier versions of composites. However, these early attempts often fell short of the stringent performance requirements set by the railroad industry, leading to a perception that non-wooden ties were inferior and unreliable.
But the tide is turning. Advancements in material science, manufacturing processes, and engineering design have paved the way for a new generation of composite ties that are challenging the status quo.
Evertrak 7000: A Game-Changer
Companies like Evertrak are transforming the railroad industry by developing composite ties that outperform traditional wood alternatives. The key breakthrough has been their glass fiber reinforced polymer (GFRP) technology, which combines high-strength glass fibers with recycled plastic to create ties that match wood’s strength while offering superior durability and environmental benefits.
Through a strategic partnership with Owens Corning, a leader in building materials, Evertrak has optimized their GFRP technology. Their collaborative research has perfected the extrusion process to maintain ideal glass fiber dimensions, ensuring optimal structural integrity in the composite ties. The success of this innovation is evident in their adoption by major operators like Union Pacific, which has begun replacing wood ties with Evertrak products.
The railroad industry faces mounting pressure to reduce its environmental impact while improving operational efficiency. Composite ties address both challenges through their exceptional durability and reduced maintenance needs, offering significant long-term cost savings. Products like the Evertrak 7000 represent a leap forward in rail infrastructure technology.
This transition to composite ties symbolizes more than just a material replacement – it represents the industry’s embrace of innovation and sustainability. As more operators recognize the advantages of this technology, we can expect an increasing shift away from wooden ties. With companies like Evertrak leading this transformation, the railroad industry is well-positioned to meet modern infrastructure challenges while reducing its environmental footprint.
Evertrak 7000 vs. Wood Ties: A Comparative Analysis
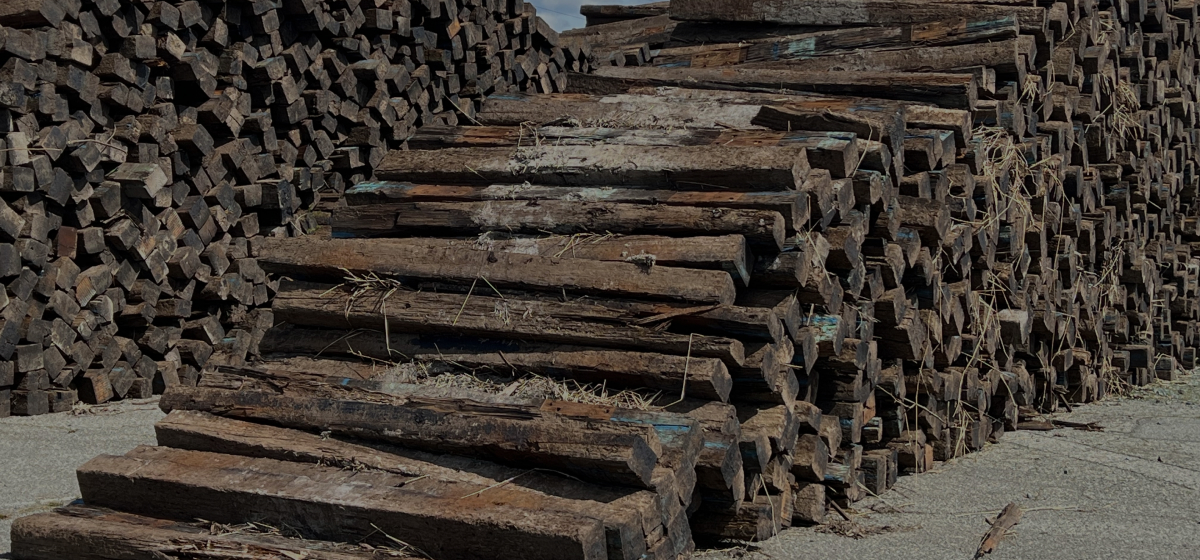
Industry estimates indicate that approximately 22 million wood ties need to be replaced annually, emphasizing the vast potential for innovative solutions like Evertrak 7000. When compared to traditional wood ties, the Evertrak 7000 offers several compelling advantages:
1. Strength and Durability
Evertrak 7000 ties are engineered to match the strength of wood ties, with validated fatigue models showing they perform at 3x the AREMA MOR standard for composite ties. In high-decay regions, Evertrak ties are expected to last up to 50 years—five times longer than wood ties.
2. Environmental Sustainability with Recycled Materials
Each mile of Evertrak ties saves 1,300 trees and diverts 585,000 pounds of plastic from landfills and oceans. By using recycled materials and eliminating the need for harmful preservatives like creosote, Evertrak ties offer a more sustainable alternative to wood.
3. Cost-Effectiveness
While the upfront cost of composite ties may be higher than wood, their extended lifespan and reduced maintenance requirements result in a lower total cost of ownership over time. Evertrak ties can help railroad operators save on replacement and labor costs, while minimizing service disruptions.
Busting the Myths About Composite Ties
Despite the proven benefits of composite ties, some misconceptions still persist in the industry. Let’s address a few common myths:
Myth 1: Composite ties are not as strong as wood.
Fact: Evertrak 7000 ties are engineered to match the strength and stiffness of wood ties, with rigorous testing and real-world performance data to support this claim.
Myth 2: Composite ties are too expensive.
Fact: While the initial cost may be higher, the extended lifespan and reduced maintenance needs of Evertrak ties result in significant long-term savings for railroad operators.
Myth 3: Composite ties are unproven.
Fact: Evertrak has installed over 100,00 composite ties with zero claims, demonstrating our ties’ reliability and performance in real-world conditions.
A Sustainable Solution for Railroad Infrastructure
As the railroad industry grapples with the challenges of sustainability, efficiency, and safety, composite ties like the Evertrak 7000 offer a compelling solution. By partnering with industry leaders like Owens Corning, Evertrak is driving innovation and setting new standards for performance and environmental responsibility.
The shift towards composite ties represents a significant opportunity for railroad operators to modernize their infrastructure, reduce their environmental impact, and achieve long-term cost savings. With products like the Evertrak 7000 leading the way, the future of rail infrastructure is looking brighter—and greener—than ever before.